Informationen
- Genel Bilgiler
INFORMATION
DIAMOND AND CBN
GRINDING WHEELS
Diamond and cubic
boron nitrit (CBN) are the hardest known abrasives available today.
For this reason they are suitable for materials that could be
machined with conventional abrasives (silicon carbide,corundum) only
with great difficulty.
Both abrasives have
the same crystal structure. Diamond consist of pure carbon; CBN
however, is composed of boron and nitrogen.
Despite their physical
relationtionship, their chemical behavior differs. Diamond ;
because of it's hardness and wear resistance, is an
important abrasive for grinding hard and brittle materials like
tungsten carbide, metallized alloys and oxide ceramics. Cubic boron
nitride is used for grinding hard and tough materials like hardened
steels, high speed steels and chilled cast iron.
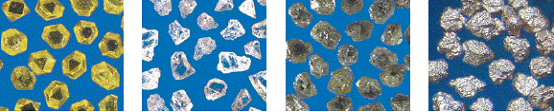 |
CBN |
Mono Crystal Diamond |
Poli
Crystals Diamond
|
Metal Coated Diamond
|
With CBN
grinding wheels:
-High
speed steels(HSS)
-Alloyed steels(HRc³58)
-Special alloys
-Stellite
When a
grinding problem needs to be solved, the question of which abrasive
is best suitable for a given material is always of prime importance.
Frequently it is advisable to run basic trials.
Another difference between these two abrasives is their thermal
stability. In the presence of oxygen, diamond burns at
temperatures above 700 °C, while CBN remains stable up to 1400 °C.
The lifetime of grinding tools can be much longer by using pure oil
or emulsion of oil.
Diamond and CBN types of
various shapes, strengths and sizes are available, depending on the
bond, the material and grinding process.
GRIT SIZES
Grit
size as well as quality of abrasive determine to a
wide range the performance of the wheel, the material removal
rate,the efficiency of the grinding process and the quality of the
obtained surfaces.
In
order to quarantee perfect cutting qualities at prescribed
surface finishes, accurate grit calibration is essential. This is
achieved by sieving and precision sedimentation.
Through continuous research and development of our products we are
always able to use optimal types with respect to the bond.
With
coarser grains, the grinding performance is greater. On the other
hand, finer grains increase the finish quality, but decrease the
stock removal capability.
MicroDiam grinding tools are manufactured and marked in accordance
with FEPA standards.
FEPA-standard |
US-standard
ASTM-E-11-70
(meshes per inch)
|
ISO R
565/1972 Mesh
widths(um) |
D
|
CBN |
|
|
D301 |
B301 |
50/60 mesh |
300/250 |
D251 |
B251 |
60/70 mesh |
250/212 |
D213
|
B213 |
70/80 mesh |
212/180 |
D181 |
B181 |
80/100
mesh |
180/150 |
D151 |
B151 |
100/120
mesh |
150/125 |
D126 |
B126 |
120/140
mesh |
125/106 |
D107 |
B107 |
140/170
mesh |
106/ 90 |
D 91 |
B 91 |
170/200
mesh |
90 / 75 |
D 76 |
B 76
|
200/230
mesh |
75 / 63 |
D 64 |
B 64 |
230/270
mesh |
63 / 53 |
D 54 |
B 54 |
270/325
mesh |
53 / 45 |
D46 |
B46 |
325/400
mesh |
45 / 38 |
BONDS
Wheel
performance and the economy of the grinding operation are determined
to a large extent by the correct choice and the careful manufacture
of the bond, as well as by the quality and the size of abrasive.
The bond and the diamond grit form the impregnated diamond section
of the wheel. Apart from the diamond grit size and concentration,
the bond itself decides the grinding performance of the wheel.
Generally, harder bonds give longer wheel life.
Material removal rate and wheel life are contradictory. As MRR
increases, the wheel life decreases.
A grinding operation without wheel wear is impossible.
Depending on the grinding process and the application requirements,
MicroDiam grinding tools are offered with various types of bonds.
Resin bonds & Metal bonds
RESIN
BONDS
Resin bonds are known for their high cutting performance.Resin bonds
are recommended for medium, fine and super-fine grinding. They are
especially suitable for material removal and can be used for dry and
wet grinding.
METAL
BONDS
The abrassion capacity
of such wheels is somewhat lower than with resin bonds. Due to their
wear resistance which in some cases is significantly higher, they
are suitable for grinding processes which are difficult to manage
with resin wheels.
Metal bonds without cooling are recommended only in exceptional
cases for small contact surfaces.
Bond
Hardness |
<HARD -------- SOFT > |
SYMBOL |
J L
N P
R |
SB
-->
Wet grinding
SYB -->
Wet grinding, high material removal rate
SKB -->
Dry grinding, very hard bond
CSP -->
Very hard bond, high requirement for profil and edge stability
CONCENTRATION
Concentration is
the ratio between the weight of diamond or CBN in carats(0.2g) and
the weight of a cubic centimeter; of bond. In accordance with FEPA
standards, concentration "100" relates to a diamond content of 4,4
carats in a bond volume of 1 cubic centimeter; all other
concentrations are proportional.
The concentration has a considerable
influence on the cutting qualities and the life of a wheel; it also
determines to a large extent the price of the wheel.
Normal concentrations for diamond and CBN
wheels:
Diamond |
Carat/cm3 |
CBN |
Carat/cm3 |
C 50
C 75
C 100
C 125 |
>=2.2ct/cm3
>=3.3ct/cm3
>=4.4ct/cm3
>=5.5ct/cm3 |
V 120
V 180
V 240
V 300 |
>=2.09ct/cm3
>=3.13ct/cm3
>=4.18ct/cm3
>=5.22ct/cm3 |
WE GUARANTEE TO CONSIDER FOR
OUR PRODUCTS THE VOLUMES OF DIAMOND AND CBN CORRESPONDING TO THESE
STANDARDS.
THE
MECHANICS OF THE GRINDING PROCESS
Grinding is a process in which chips are removed from the surface of
the workpiece with the aid of abrasive materials. In contrast to
other metal cutting processes such as turning, milling, etc., the
material is removed by cutting edges of undefined geometry.
Basically a distinction must be made whether the grinding agent is
bonded in a grinding tool or whether it exists in the form of loose
grits such as grinding paste for polishing.
The selection of the optimum grinding wheel depends on the machine
(grinding process, adjustment facilities, stability)and the material
(hard and brittle materials such as tungsten carbide, ceramics or
hard and tough materials such as HSS, chilled cast iron,etc.)
The specifications are influenced by the following parameters:
Grit size:Required
surface finish, grinding process
Grinding agent:Material, e.g. diamond for tungsten carbide and
CBN for HSS
Concentration:Contact surface grit size, grinding process
Bond:Grinding agent, grit size
SELF-SHARPENING
When a wheel works under optimum conditions, the surface largely
sharpens itself by splintering worn grits and exposing new ones. If
the grinding forces become too high because of an excessive feed
rate, low speed of the wheel or high table speed, the abrasive grain
can drop prematurely out of the bond.
With slow feed rates, high speeds or slow table speeds, the grinding
forces are lower. This can result in flattening of the abrasive
grains and unfavorable results.
In both cases the self-sharpening effect can be improved through
corresponding modification of the machining parameters.
THE
G RATIO
The wear characteristic of a grinding
wheel is expressed by the "G" ratio.
(cm3)
G=Removed material
vol.
Volume of rim wear
(cm3)
When the volume of the grinding wheel
and the wheelprice are known, the cost-effectiveness of a grinding
operation can be determined with the aid of the
G-value, taking into account also personnel and machine costs.
RECOMMENDED PERIPHERAL SPEED
Dry grinding should
only be applied on materials with good thermal conductivity. In the
connection with diamond, heat developement should be avoid by an
adequate cooling.
Generally, CBN should
be used with a higher peripheral speed. A condition for that
is an efficient coolant and a stable machine. The wheel's life and
the surface quality may be improved.
Abrasives |
Bond type
|
Wet grinding
|
Dry grinding
|
Diamond |
Resin
Metal |
20-30
15-25 |
10-20
10-15 |
CBN |
Resin
Metal |
40-80
40-80 |
15-30
10-20 |
The achievable surface depends on the
grit size, the grinding operation and consequently also on the
material. The table below relates to general tool grinding (cross
grinding) with diamond and CBN in resin bonded wheels on the
tungsten carbide grade K20 or HSS
In order to achieve an equivalent
surface quality with CBN, the grit size has to be smaller by two or
three fractions.
FEPA
grit size
|
Mean
roughness Ra (um) |
Surface
quality |
Grinding process |
Diamond CBN |
Diamond CBN |
N |
------- B301
------- B251
------- B213
------- B181
------- B151
------- B126 |
-------- 2,10
-------- 1,77
-------- 1,41
-------- 1,12
-------- 0,75
-------- 0,66 |
N8
N8 - N7
N7
N7 - N6
N6
N6 |
Very
rough grinding |
D181 B107
D151 B91
D126 B76 |
0,53 0,53
0,50 0,50
0,45 0,45 |
N6-N5
N6-N5
N6-N5 |
Rough
grinding |
D107 B64
D91 B54
D76 B46 |
0,40 0,40
0,33 0,33
0,25 0,25 |
N5
N5-N4
N5-N4 |
Semifinish
grinding |
D64 ----
D54 ----
D46 ---- |
0,18 ----
0,16 ----
0,15 ---- |
N4
N4-N3
N4-N3 |
Fine
grinding
|
MD25 ----
MD20 ----
MD10 ---- |
0,12 ----
0,05 ----
0,025 ---- |
N3
N3-N2
N2-N1 |
Ultrafine grinding |
|
N1 |
N2 |
N3 |
N4 |
N5 |
N6 |
N7 |
N8 |
Ra(um) |
0,025 |
0,05 |
0,10 |
0,2 |
0,4 |
0,8 |
1,60 |
3,20 |
Ra(um) |
0,500 |
0,80 |
1,25 |
2,5 |
5,0 |
8,0 |
16,0 |
32,0 |
Ra(um) |
0,400 |
0,63 |
1,00 |
2,0 |
4,0 |
6,3 |
10,0 |
16,0 |
RECIPROCAL GRINDING AND DEEP GRINDING
In the reciprocal grinding
process,table speeds of ³6m/min and feed rates of £0.05mm
are commonly used. Because the grinding rim recontacts the workpiece
with each run-out, it is subjected to numerous contact shocks, the
severity of which depends on the total material to be removed and
the selected feed rate.
In deep grinding operations the table speed is considerably reduced
and in turn the feed rate is selected as high as possible, i.e. the
grinding body is subjected to very few contact shocks.
The advantage of deep grinding is not necessarily the shorter
grinding time or the higher stock removal capacity. Important is the
fact that the grinding rim contacts the material only twice with
very slow table movement. This significantly reduces the wear on the
grinding rim and correspondingly increases its economy.
A prerequisite for deep
grinding is a stable machine with sufficient spindle capacity and
efficient cooling.
TRUING AND DRESSING OF DIAMOND AND CBN GRINDING WHEELS
The purpose of truing diamond or CBN wheels is to guarantee the
geometry of the wheel and to eliminate true or plane running errors.
Wheels that have become deformed due to uneven wear or which do not
run true, can be reshaped or trued again.For this purpose the
surface of the grinding rim is brought to the desired shape by means
of silicon carbide or corundum wheels. In the case of CBN wheels a
multigrit diamond dressing tool can also be used.
Particularly for CBN wheels these preparations do not meet the
requirements. Due to the difference in the chip formation when
grinding highspeed steels or similar materials, the CBN grain must
penetrate deeper into the material and the chip requires a larger
chip space for removal.
Dressing(sharpening)
of the grinding rim is, therefore, an absolute necessity. The wheels
should prefefably be dressed directly on the machine by pressing a
sharpening stone against the grinding rim of
the rotating wheel. Minimal coolant flow is
beneficial, in any case the stone should be at least moistened.
Optimum grinding performance is achieved if the wheel is
subsequently used in the same sence of rotation.The same applies to
diamond grinding wheels.
Diamand and CBN tools, being expensive, require more attention and
care in handling.
-The use of COOLANT is generally for faster cutting, better surface
finish and longer wheel life. Wet grinding should be used wherever
possible although resin bond wheels can be used dry. Alkaline
liquids for resin bonds sould be avoided.
When CBN wheels are used wet, optimum performance is achieved with
pure oil. If an emulsion has to be used, 20% oil will give good
results in many applications.
Pure water or water with rust inhibitor will damage the CBN
grit, and should be avoided.
Use a high horsepower and vibration-free machine.
The wheels are supplied balanced, but it is recommended to recheck
the balance.
-Check the spindle and the back plate of the grinding machine
to ensure their precise runout.
-Check the runout of the wheel, before and after closing the
mounting screws. With cup wheels, use shims to make the face run
true. Straight wheels are to be shifted on the spindle, tapping them
lightly, until the wheels run out.
-Corner grinding is generally not recommended; the corner will round
off fast and might cause chipping.
-If you remove the wheel from the machine to month again, you must
mark the wheel and the flange. When you want to month the wheel
again, you have to press until the marks are across from
eachother.
-Avoid
excessive pressure, excessive infeed and excessive table movement.
Please
give the following details:
1-Type
of abrasive(diamond or CBN) and type of wheel
2-Dimensions:
a-Wheel diameter
b-Width and thickness of the abrasive layer
c-Hole
size
3-Required surface finish
4-CBN
or diamond concentration
5-Bond
type
6-Wet
and dry grinding (for wet grinding , please specify type of
coolant)
7-Materials to be ground
8-Details regarding the machine,e.g.power
9-Type
of work-off-hand or mechanical grinding
10-Desired
cutting speed, in- feed and table speed
THE ECONOMICAL WORKING SPEEDS OF
DIAMOND AND CBN
DIAMOND
WHEELS |
CBN
WHEELS |
. |
Resin
Bonds |
Metal
Bonds |
. |
Resin
Bonds |
Metal
Bonds |
Grinding
Type |
Wet
grinding |
Dry
grinding |
Wet
grinding |
Dry
grinding |
Grinding
Type |
Wet
grinding |
Dry
grinding |
Wet
grinding |
Dry
grinding |
Surface
Grinding |
20-30
m/s |
.
|
15-25
m/s |
. |
Surface
Grinding |
22-35
m/s |
.
|
20-25
m/s |
. |
Internal
cylindrical
grinding |
16-25
m/s |
15-20
m/s |
15-20
m/s |
10-15
m/s |
Internal cylindrical
grinding |
20-30
m/s |
18-25
m/s |
15-25
m/s |
15-20
m/s |
External
cylindrical
grinding |
20-30
m/s |
. |
15/25
m/s |
. |
External
cylindrical
grinding |
22-35
m/s |
. |
20-25
m/s |
. |
Tool
Grinding |
18-28
m/s |
15-20
m/s |
15-20
m/s |
10-15
m/s |
Tool
Grinding |
20-30
m/s |
18-25
m/s |
15-20
m/s |
5-25
m/s |
|